Cuando estaba en la carrera tuve un montón de horas de prácticas con el microscopio. En ellas mirábamos rocas en lámina delgada y aprendíamos a reconocer las propiedades ópticas de los minerales y las diferentes texturas.
Cada vez que cogíamos una de aquellas láminas delgadas el profesor nos advertía que la tratásemos con cuidado y cada vez que se oía el sonido de una de aquellas láminas rebotando en el suelo, estoy seguro de que el profesor perdía una semana de vida.
No comprendí hasta que salí de la universidad el por qué de esa preocupación. Había dos razones fundamentales. Una era la práctica, que era el poder encontrar otra lámina con la textura o el mineral que pretendían enseñarnos y que fuese didáctico. La segunda, y de la que voy a hablar, es por la fabricación de las láminas delgadas.
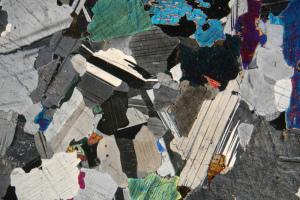
El primer paso es realizar el primer corte a partir de la roca que llega al laboratorio. En ella se ha podido realizar una indicación de por dónde queremos hacer la lámina o una zona específica que queremos estudiar. Si no queda a la elección de quien la fabrica. En este paso se llega a cortar un prisma que tiene una de sus caras el área que ocupa la lámina de vidrio que posteriormente se utilizara.
En ocasiones es necesario el reforzar la muestra con una resina, porque su alteración o su estado es tan endeble que se puede deshacer, literalmente, en nuestras manos, y la muestra necesita un tratamiento previo antes de seguir.
Tras este primer rebaje se procede al pulido. Este se realiza con la función de que una de la caras de la roca quede lo más plana posible. Para realizar esta labor se utilizan diferentes abrasivos en polvo, normalmente alúmina o carborundo, ambos aleaciones artificiales con una dureza próxima a la del diamante. Para realizarlo solo es necesario poner el abrasivo en una plancha y mezclarlo con agua para que forme una pasta. Se toma la muestra y se frota sobre ella haciendo giros. Esto puede realizarse en tornos, similares a los de los escultores de arcilla, girando a alta velocidad para que se haga mucho más rápido.
Lo habitual es pasar la muestra por varios abrasivos, desde el más grueso al más fino, para ir logrando un acabado cada vez mejor. El acabado final, el plano perfecto, es una superficie pulida, con un reflejo en espejo, donde los minerales brillan. Este acabado es el que se utiliza para el estudio de minerales opacos y metálicos, pero eso es otra historia.
Ahora que tenemos una superficie plana hay que pegarla sobre una lámina de vidrio. Para ello es necesario un pegamento específico (una resina epoxy) o un bálsamo (el más utilizado es el bálsamo de Canada). Se unta la superficie lisa y se extiende sobre ella como si fuera mantequilla en una rebanada de pan. Se debe colocar una capa homogénea y que cubra toda la superficie y de ahí a la lámina. Este momento es crítico para que no queden burbujas de aire entre el pegamento y la lámina de vidrio ya que aparecerían en el posterior estudio en el microscopio y es muy molesto. Una vez que comprobamos que no hay burbujas se coloca en una placa calefactora y se pone presión encima. La temperatura no es muy alta, de unos 50ºC, y no mucha presión, pero esto hará que el pegado sea mejor y más rápido.
Tras unos treinta minutos se comprueba el estado y se deja enfriar, si se ve seco, antes de continuar.
Una vez fría tenemos una lámina de vidrio con un taco de roca pegado a ella. El siguiente paso es cortar. Yo utilizaba una máquina que me permitía realizar un corte hasta los 0,5 mm de espesor, pero esto aún es demasiado grueso para estudiarlo por lo que hay que rebajarlo y la manera es mediante un pulido. En una máquina se pueden alcanzar hasta los 0,1 mm, que aún es mucho espesor.
A partir de este momento vuelve el trabajo manual. En las mismas condiciones en las que se ha realizado el primer pulido de la roca se realiza este, eso sí, con mucho más cuidado y evitando abrasivos muy gruesos ya que el pulido que necesitamos es muy fino y un par de pasadas por los gruesos podrían destruir todo el trabajo que hemos realizado hasta ahora.
Mientras se realiza este pulido final entra en escena el microscopio por primera vez, en este caso para determinar si la lámina está bien o necesita algo más de trabajo. En principio, una lámina está terminada cuando se alcanzan los 0,03 mm de espesor, que para comparar es aproximadamente 1/3 del espesor de un cabello humano. Con este espesor se conocen diferentes propiedades ópticas de los minerales que permiten reconocerlos y estudiarlos y que los hace únicos respecto a otros con características muy similares y que a lo mejor, en un primer vistazo, han quedado desapercibidos.
Todo el proceso lleva, aproximadamente, seis horas de trabajo si la roca está bien y se porta. Otras en peores condiciones pueden llevar varios días de trabajo. Ahora entiendo mejor a mis profesores.