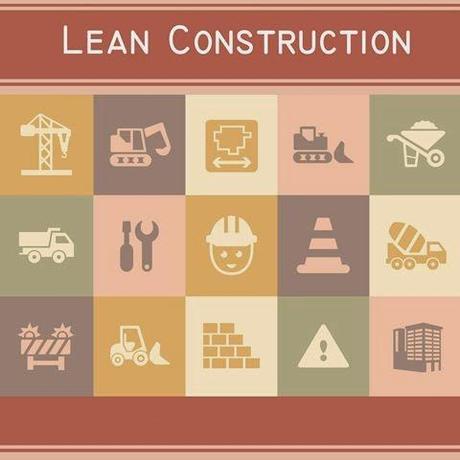
Esta tendencia tiene que cambiar. "Afortunadamente", ya no tenemos la prisa que teníamos, ahora hay tiempo pensar, proponer, cambiar, programar, definir y por último ejecutar con garantías. Hemos de abandonar los plazos irreales, verdadero cáncer de la siniestralidad laboral, la improvisación, germen de resultados no esperados y por supuesto hemos de profesionalizar el sector por medio de formación específica más exigente a la que actualmente contempla la Ley.
Para lograr todo esto, lo fundamental es empezar por un cambio de mentalidad, desaprender lo aprendido para comenzar a interiorizar nuevas formas de trabajar, más organizadas, más protocolizadas , más consecuentes, en definitiva más responsables. Hay que pensar en la actividad como en una forma de vida, no como en una herramienta para el enriquecimiento tal y como ha ocurrido en tiempos pasados. Debemos entender la actividad como enriquecedora para todos los agentes participantes en el proceso, desde proyectista, el contratista, los subcontratistas hasta el cliente y el usuario final.
Esta experiencia enriquecedora puede conseguirse por medio de la filosofía LEAN cuya base es la mejora continua con el fin de crear valor para el cliente y eliminar los desperdicios durante el proceso productivo.
La filosofía LEAN no es nada nuevo. Al principio del siglo pasado, Henry Ford comenzó a fabricar los primeros coche en linea de producción. Este hito supuso un acicate hacia la mejora de la producción en la industria. Posteriormente, tras la Segunda Guerra Mundial, fue cuando la empresa Toyota basándose en la experiencia de Henry Ford desarrollo el sistema LEAN Production para crear sus automóviles con menos capital, menos esfuerzo humano, menos espacio y menos tiempo para fabricar con menos defectos. Esto es precisamente lo que proporciona el sistema LEAN, una serie de herramientas que contribuyen a una mayor colaboración entre los diferentes agentes que intervienen a lo largo de todo el ciclo de vida de un producto o servicio.
Esta filosofía ha sido aplicada con éxito en un sinfín de casos durante la totalidad del siglo pasado, pero siempre enfocado a procesos productivos dentro de la industria y en particular en la del automóvil.
En base al éxito obtenido, en los últimos tiempo se ha trabajado para "exportar" esta filosofía a otros modelos de producción. En este sentido los que más nos interesan y en los que baso este post es el Lean Office (perfectamente aplicable a la fase de proyecto) y el Lean Construction (aplicable para el resto del proceso edificatorio).
En cualquiera de sus manifestaciones la filosofía LEAN, se fundamenta en 5 pilares principales, también denominada la metodología de las 5 "S". Esta metodología nació en Toyota en los años 60 en un entorno industrial, con el objetivo de lograr lugares de trabajo mejor organizados, más ordenados y más limpios, de forma permanente, para conseguir una mayor productividad y un entorno laboral mejor y más seguro. La expresión 5 "S" proviene de las iniciales de 5 palabras japonesas: Seiri (Organizar), Seiton (Ordenar): Seiso (Limpieza), Seiketsu (Estandarización) y Shitsuke (Hábito).
Para aplicar todo lo anteriormente expuesto, es importante conocer la base y el espiritu de esa metodología. A este espíritu se le ha llamado KAIZEN. Este es la herramienta fundamental sobre la que gira el éxito de la implantación del sistema. En Japones KAI significa "cambio" y ZEN significa "bueno". En definitiva, cambio hacia la mejora y se resume en 10 ideas concretas:
- Abandonar las ideas fijas, rechazar el estado actual de las cosas.
- En lugar de explicar lo que no se puede hacer, reflexionar sobre como hacerlo.
- Realizar inmediatamente las buenas propuestas de mejora.
- No buscar la perfección, mejorar el 60% desde ahora.
- Corregir el error inmediatamente "in situ"
- Encontrar ideas en la dificultad.
- Buscar la causa real. respetar los "5 por qués" y después buscar la solución .
- Tener en cuenta las ideas de 10 personas en lugar de esperar la idea genial de una sola.
- Probar para después validar.
- La mejora es infinita.
Por: Mario Ortega Pascual.
Más info: Introducción a Lean Construction