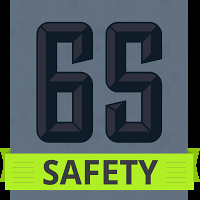
Debemos tener el convencimiento de que la prevención no es una carga dentro del proceso productivo, ni siquiera una prioridad, sino que es un VALOR indiscutible que SIEMPRE ha de estar presente desde el inicio de la concepción de cualquier proyecto. La prevención NUNCA hemos de considerarla una prioridad, ya que las prioridades pueden cambiar con el tiempo, mientras que los valores son principios permanentes que nos permiten orientar nuestro comportamiento en la dirección de los objetivos a alcanzar. Los valores representan ideales, sueños y aspiraciones, que no dependen de las circunstancias del entorno.
Los valores valen por sí mismos. Son importantes por lo que son, lo que significan y lo que representan, y no por lo que se opine de ellos. Los valores fomentan la actitud para actuar en cualquier momento con sensatez y coherencia.
Los valores se traducen en pensamientos, conceptos e ideas, pero lo relevante es el COMPORTAMIENTO final, que de esos pensamientos, conceptos e ideas, hacen las personas.
Y aquí es donde pone el foco el “Lean”, en el factor psicosocial, en el cambio de paradigma, de manera que exista una sensibilización que permita el convencimiento de los intervinientes en el proceso, poniéndose al servicio de la técnica “LEAN”, y dejando de lado las imposiciones habituales que han reinado en nuestro sector. Esto no es una tarea sencilla, ni de rápida aplicación, pero con mucha COMUNICACIÓN, entornos COLABORATIVOS y tiempo, se puede conseguir. Digamos que es una herramienta del presente para realizar una inversión de futuro. “Por hacer un símil, es como el pacto por la educación, que tanta falta hace en nuestro país”
En base a esto, concluimos que:
- La seguridad ha de ser lo primero, pero no como una prioridad, sino como un VALOR.
- “Lean” es 75% social y 25 % técnica
- La seguridad no es independiente de producción, sino que forma parte de ella.
- Los trabajadores empatizan más con los hechos que con las palabras. (Las palabras son importantes, pero deben ir acompañadas de hechos)
- El enfoque de culpabilidad no previene accidentes.
- Objetivo cero lesiones (sea posible o no)
- La mayoría de los accidentes se pueden prevenir.
- La mayoría de los accidentes ocurren debido a condiciones inseguras y comportamiento inseguro.
Como ya he indicado, “Lean” es 75% social y 25 % técnica, por lo tanto, cuando implantamos la metodología “LEAN” a cualquier campo de aplicación, debemos conocer esa técnica y las herramientas comunes que articulan esta filosofía de trabajo.
- Herramientas Lean aplicables a la seguridad son :
- 5S
- LPS “Last Planner System”
Las 5 ”S”
Esta nomenclatura proviene de las iniciales de 5 palabras japonesas: Seiri (Seleccionar), Seiton (Ordenar), Seiso (Limpieza), Seiketsu (Estandarización) y Shitsuke (Hábito).
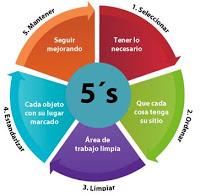
- Seiri – Seleccionar y eliminación de elementos innecesarios del puesto de trabajo
- Seiton – Orden correcto para cada elemento y establecimiento de límites
- Seison – Brillo, esplendor y limpieza en el lugar de trabajo. Aplicar limpieza como estándar de inspección.
- Seiketsu - Estandarizar buenas prácticas en el área de trabajo y compartir informaciones.
- Shitsuke - Mantenimiento de resultados a través de la autodisciplina.
6. SEGURIDAD – Como valor siempre presente.
Centrándonos en esta “Sexta S” hemos de tener muy presente el archiconocido “Principio de PARETO” o “Regla del 80-20” por el que determinamos que el 80% de los efectos son producidos por el 20% de las causas. Y es en ese punto donde debemos focalizar nuestros esfuerzos, en detectar el 20% de las causas que producen el 80% de los accidentes. Se ha demostrado si se controlan adecuadamente las condiciones de trabajo, entorno, maquinaria, trafico etc… la accidentalidad puede disminuir hasta ese 80%, debiéndose el otro 20%, a acciones por comportamiento inseguro.
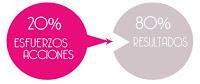
- Formación y entrenamiento
- Monitorización continúa de procesos.
- Poka Yoke (a prueba de fallos)
- Benchmarking... (Comparación)
- Flujo continuo
- Estandarización de los procesos de trabajo
- Organización en el trabajo.
Es fundamental conocer los datos de partida para ser selectivo en nuestras acciones y de esta manera comenzar a abordar los problemas de manera que con el mínimo nº de acciones obtengamos el máximo beneficio. A nivel de seguridad, en términos generales, podemos tomar como base para iniciar nuestro trabajo, los datos que a continuación adjunto:
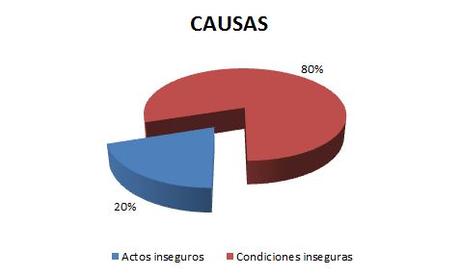
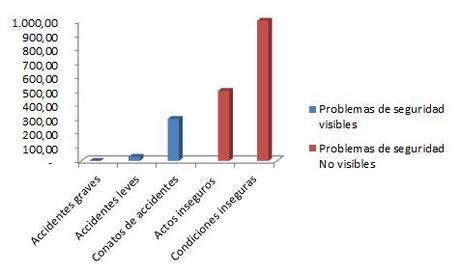
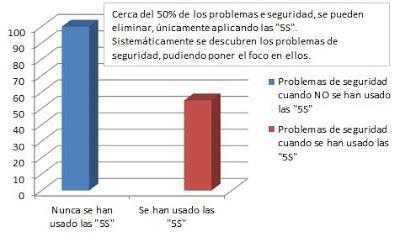
LSP "Last System Planner"
Está herramienta está enfocada a realizar un seguimiento monitorizado de la planificación general de producción o PLAN MAESTRO. Como ya hemos visto, la seguridad ha de ser una parte fundamental de la producción por lo que hemos de integrarla, planificarla y auditarla de igual manera que lo hacemos con la asignación de recursos, suministro de materiales, afecciones entre actividades o cualquier otro aspecto vinculado con la producción de la obra. Hemos de considerar la prevención, una “actividad” que genera flujo y por tanto una vez haya sigo realizada permita poner en marcha las actividades dependientes de ella que generan transformación.
“LPS crea y mejora la predicción del flujo de trabajo en los proyectos. Los resultados son fruto del trabajo en equipo a través de una serie de conversaciones de planificación. Estas conversaciones se encargan de diseñar y activar la red de compromisos indispensables para identificar la necesidades para alcanzar una serie de hitos, para que el trabajo esté listo, asegurándose de que una persona se compromete a realizarla, y por último, aprender de la propia experiencia” (Lean Project Consulting)
La forma de gestionar LPS es por medio de una planificación en cascada donde contamos con tres niveles de detalle:
- PLAN MAESTRO o Planificación General: Se trata de un diagrama de Gantt al uso pero consensuado entre los integrantes en el proceso constructivo, en el que se definen los trabajos principales así como sus vínculos, generando de esta manera el COMPROMISO GENERAL
- PLAN INTERMEDIO o Planificación a 6 semanas vista: En la que se realiza, mediante reuniones colaborativas, un análisis de actividades, detectando las restricciones producidas por las actividades que generan flujo (burocráticas, PREVENTIVAS, transportes, etc…) para que de esta manera puedan ser realizadas las actividades que generan transformación (productivas)
- PLAN SEMANAL o Planificación a 1 semana vista: en el que se gestiona, también mediante reuniones que fomenten el dialogo, el COMPROMISO final de las partes intervinientes en el proceso.
Hasta aquí esta introducción al LEAN SAFETY, esperando haya sido ilustrativo e inspirador para que poco a poco vayamos introduciéndonos en esta metodología, que espero sea implantada progresivamente, para reconstruir de manera responsable un sector herido, pero que sin duda es necesario para el buen funcionamiento de nuestra economía.