Estas son algunas de las apreciaciones de directivos ante el programa 5 S.
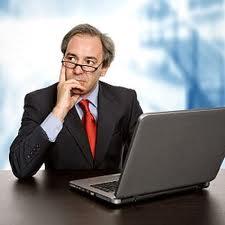
PARADIGMA 1 “Es necesario mantener los equipos sin parar”
La dirección ante las presiones de entregar oportunamente y en cantidades suficientes los productos que se fabrican, no acepta fácilmente que un puesto de trabajo es más productivo cuando se mantiene impecable, seguro, en orden y limpio. Se considera que la limpieza es una labor que consume tiempo productivo, pero no se aprecia los beneficios de ésta en ayudar a eliminar las causas de averías como el polvo, lubricación en exceso y fuentes de contaminación.
PARADIGMA 2 “Los trabajadores no cuidan el sitio”
Para qué perder tiempo, la dirección considera que el aseo y limpieza es un problema exclusivo de los niveles operativos. Si los colaboradores no poseen los recursos o no se establecen metas para mejorar los métodos será difícil que el operario tome la iniciativa. Es seguro que los trabajadores apreciarán los beneficios, ya que son ellos los que se ven afectados directamente por la falta de las 5 S.
PARADIGMA 3 “Hay muchos pedidos urgentes para perder tiempo limpiando”
Es frecuente que el orden y la limpieza se dejen de lado cuando hay que realizar un trabajo urgente. Es verdad que las prioridades de producción a veces presionan tanto que es necesario que otras actividades esperan, sin embargo, las actividades de las 5 S se deben ver como una inversión para lograr todos los pedidos del futuro y no solamente los puntuales requeridos para el momento.
PARADIGMA 4 “Creo que el orden es el adecuado no tardemos tanto tiempo...”
Algunas personas consideran sólo los aspectos visibles y de estética de los equipos suficientes. Las 5 S deben servir para lograr identificar problemas profundos en el equipo, ya que es el contacto del operario con la máquina lo que permite identificar averías o problemas que se pueden transformar en graves fallos para el equipo. La limpieza se debe considerar como una primera etapa en la inspección de mantenimiento preventivo en la planta.
PARADIGMA 5 “Sale más barato un trabajador inexperto para la limpieza”
El trabajador que no sabe operar un equipo y que es contratado únicamente para realizar la limpieza, impide que el conocimiento sobre el estado del equipo sea aprovechado por la empresa y se pierda. El contacto cotidiano con la maquinaria ayuda a prevenir los problemas, mejora la información hacia los técnicos expertos de mantenimiento y aumenta el conocimiento del operario sobre el comportamiento de los procesos.
La aplicación de las 5 S tiene sus barreras en ciertos pensamientos de los operarios:
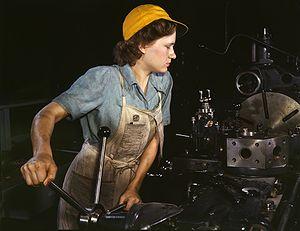
PARADIGMA 1 “Me pagan por trabajar, no para limpiar”
A veces, el personal acepta la suciedad como condición inevitable de su estación de trabajo. El trabajador no se da cuenta del efecto negativo que un puesto de trabajo sucio tiene sobre su propia seguridad, la calidad de su trabajo y la productividad de la empresa.
PARADIGMA 2 “Llevo 10 años…. ¿Por qué debo limpiar?"
El trabajador considera que es veterano y no debe limpiar, que esta es una tarea parar personas con menor experiencia. Por el contrario, la experiencia le debe ayudar a comprender mejor sobre el efecto negativo de la suciedad y contaminación sin control en el puesto de trabajo. Los trabajadores de producción asumen a veces que su trabajo es hacer cosas, no organizarlas y limpiarlas. Sin embargo, es una actitud que tiene que cambiar cuando los trabajadores empiezan a comprender la importancia del orden y la limpieza para mejorar la calidad, productividad y seguridad.
PARADIGMA 3 “Necesitamos más espacio para guardar todo lo que tenemos.”
Esto sucede cuando al explicar las 5 S a los trabajadores, su primera reacción ante la necesidad de mejorar el orden es la de pedir más espacio para guardar los elementos que tienen. El frecuente comentario es “……….jefe necesitamos un nuevo armario para guardar todo esto…….”. Es posible que al realizar la clasificación y el ordenamiento de los elementos considerados, sobre espacio en los actuales armarios y la mayoría de los elementos sean innecesarios
PARADIGMA 4 “No veo la necesidad de aplicar las 5 S”
Puede ser muy difícil implantar las 5 S en empresas que son muy eficientes o muy limpias como en el caso de las fábricas de alimentación, productos personales o farmacia. Sin embargo, no todo tiene que ver con la eliminación de polvo o contaminación. Las 5 S ayudan a mejorar el control visual de los equipos, modificar guardas que no dejan ver los mecanismos por guardas plásticas de seguridad que permitan la observación del funcionamiento de los equipos: o la aplicación de las 5 S en el cuidado de nuestras mesas de trabajo y escritorios,…
Un saludo.