Introducción
Con el fin de que los vehículos eléctricos sean competitivos y representen una verdadera opción, que sea una alternativa realista a los automóviles dotados de motor de combustión, los vehículos eléctricos deben de ofrecer unas prestaciones de aceleración y velocidad al menos semejantes a las que ofrecen los automóviles de combustión. Dichas prestaciones se traducen en la potencia de entrega del grupo motopropulsor eléctrico.
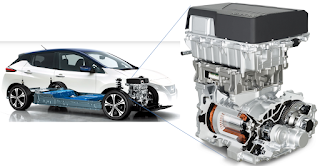
Un motor eléctrico es un transductor de energía, es decir, recibe energía eléctrica y la transforma en energía mecánica, luego la transmisión y las ruedas volverán a transformar la energía mecánica en energía cinética que representará la velocidad del vehículo. Lógicamente, al imaginar un automóvil, se entiende que es una masa de alrededor de 1500 kg, que puede acelerar con soltura hasta alcanzar una velocidad de crucero de 120 km/h como mínimo. Para conseguir esto es necesario aplicar una potencia considerable.
En electricidad, la potencia es equivalente a la tensión eléctrica (medida en voltios) multiplicada por la intensidad del flujo de corriente (medida en amperios).
P = V X A
Si como se ha explicado, es necesaria una potencia similar a la de un automóvil de combustión para que el vehículo eléctrico sea competitivo, entonces para desarrollar una potencia de 204 CV, que equivalen a 150 kW (150.000 watios), es necesario que la batería pueda entregar una potencia eléctrica de 150 kW para que los transfiera al motor eléctrico de tracción.
Opciones para formular la red eléctrica del automóvil
Planteada la necesidad explicada en este ejemplo, surgen tres maneras principales de conseguirlo cuando aplicamos la fórmula de la potencia:
- Mediante una tensión altísima y un amperaje bajo: 150.000 W = 40.000 V X 3,75 A
- Mediante una tensión alta y un amperaje alto: 150.000 W = 400 V X 375 A
- Mediante una tensión baja y un amperaje altísimo = 150.000 W = 3.750 A X 40 V
En cada una de estas maneras la potencia que se le entrega al motor es exactamente igual y las prestaciones que va a conseguir serán, por consiguiente, las mismas. Sin embargo, dependiendo de cuál de las tres maneras se consiga, los componentes eléctricos y electrónicos y la instalación de la red eléctrica variará enormemente, así como los riesgos inherentes de fugas de corriente y peligros de electrocución.
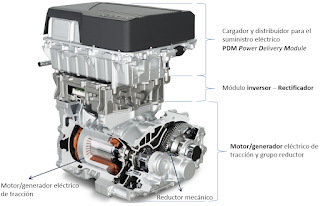
A continuación paso a describir los supuestos derivados de cada una de las tres maneras mencionadas con sus ventajas e inconvenientes característicos.
- Mediante una tensión altísima y un amperaje bajo: 150.000 W = 40.000 V X 3,75 A.
Esto requeriría elevar muchísimo la tensión de la batería o construir una batería que estaría dotada de al menos 10.000 elementos conectados en serie. De una u otra manera habría que aumentar enormemente el peso o bien de la batería o bien del convertidor de alta tensión con bobinas enormes para conseguir que la red eléctrica trabajase a 40.000 V. Además, los sistemas de aislamiento y prevención de fugas de corriente tendrían que sobredimensionarse en tamaño y peso, porque con una diferencia de potencial tan sumamente alta, enseguida habría tendencia a aparecer arcos voltaicos o chispazos, a pesar de que el aire y las superficies circundantes fuesen dieléctricas. Al final, todo esto sería un problema desde el punto de vista de ingeniería y un alto riesgo para los pasajeros y para los técnicos que tengan que intervenir a fin de reparar o dar servicio en semejante instalación eléctrica.
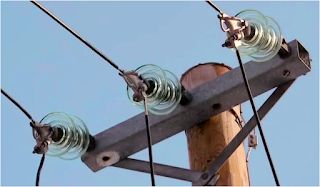
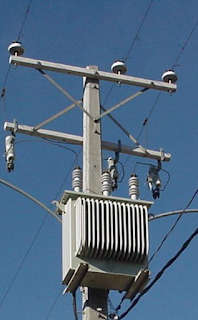
En este caso, la tensión de trabajo sería prácticamente inofensiva y no habría que preocuparse por la seguridad. Sin embargo, el hecho de trabajar con corrientes eléctricas enormes supondría dotar a la instalación eléctrica de unos cables muy gruesos. De lo contrario se carbonizarían por sobrecalentamiento. Esto supondría elevar excesivamente el peso del vehículo y el coste de la instalación eléctrica de alta tensión, ya que el cobre es de por sí un metal caro y pesado. Además, todos los componentes eléctricos involucrados en la batería y el grupo motopropulsor deberían de estar dotados de conductores muy gruesos y necesitarían carcasas y disipadores de calor muy grandes, con sistemas de refrigeración activa donde fluyese un caudal de refrigerante cuantioso. Esta opción choca de frente con un planteamiento tecnológico donde la tendencia se basa en realizar sistemas de propulsión eficientes y ligeros, y donde aplicando poca energía se puedan obtener grandes resultados
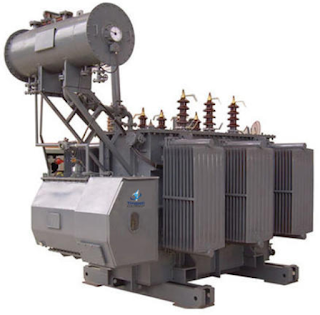
Transformador refrigerado
Por otro lado, el uso de conductores gruesos y pesados con corrientes eléctricas muy elevadas incide en pérdidas de eficiencia. Esto es debido a que cualquier resistencia eléctrica, por pequeña que sea, generaría pérdidas por calor indeseadas. Este fenómeno se explica claramente según la Ley de Ohm:
V = R X I; R = V / I; I = V / R
A poco que aumente la resistencia del circuito, cuando la intensidad que circula es muy grande, el voltaje quedará gravemente afectado por una fuerte caída de tensión y la potencia eléctrica transmitida se transformará en potencia calorífica no deseada, dando lugar a pérdidas en la energía transferida.
Esta es la explicación de por qué para transmitir grandes cantidades de energía y potencia eléctrica a destinos lejanos es necesario elevar el voltaje de trabajo de la red eléctrica enormemente (132.000 V - 380.000 V), con el objetivo de reducir las pérdidas inherentes de la corriente eléctrica.
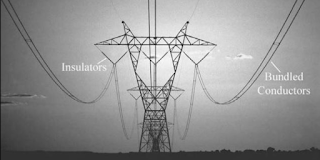
- Mediante una tensión alta y un amperaje alto: 150.000 W = 400 V X 375 A
Vistas las dos opciones anteriores, es lógico pensar que los ingenieros han encontrado un equilibrio razonable para, sin engordar demasiado el sistema de propulsión ni engendrar una red de alta tensión muy peligrosa, poder alcanzar a desarrollar un sistema de propulsión eficiente, evitando ser demasiado pesado y sin necesitar un sistema de refrigeración tan exigente como el de un motor térmico. Sin embargo, en este caso, las labores de servicio y reparación en una red de 400 V sí necesitarán un protocolo de actuación especial y diseñado para evitar riesgos por electrocución y chispas peligrosas. También serán necesarios sistemas de protección especialmente diseñados por el fabricante para detectar riesgos y cancelar la actividad de la red de alta tensión cuando exista peligro. No obstante, los valores de corriente con la que trabaja la red de propulsión eléctrica del vehículo no serán excesivamente elevados y evitarán graves pérdidas de ineficiencia originadas por pequeñas resistencias en los conductores eléctricos.
A continuación, se expone una comparativa con dos modelos, uno de combustión y otro eléctrico. El propósito es mostrar como los fabricantes más punteros de vehículos eléctricos han llegado a un compromiso equilibrado que resuelve las necesidades de prestaciones en la propulsión eléctrica, haciendo que sean automóviles competitivos frente a los de combustión.
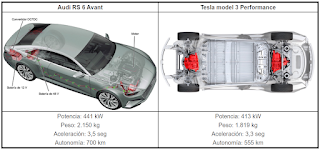
- El puerto de carga.
- El cargador de alta tensión.
- El distribuidor de alta tensión.
- El convertidor CC-CC de alta tensión a baja tensión.
- El compresor para el aire acondicionado y en algunos casos para la bomba de calor.
- La batería de alta tensión.
- El calefactor PTC de la unidad climática del habitáculo.
- El inversor/rectificador.
- La máquina eléctrica (motor/generador).
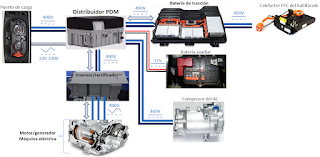
El compromiso entre la tensión y la intensidad de corriente eléctrica con la que funcionan los automóviles eléctricos son parámetros cuidadosamente estudiados y elegidos por los ingenieros con el objetivo de fabricar un vehículo que cumpla con los siguientes compromisos:
Además, estos compromisos deben de establecer una tensión y corriente de trabajo que facilite la fabricación de una batería de alta tensión cuya composición y configuración interna no haga de ella un componente demasiado complejo, pesado y difícil de controlar y monitorizar, estando lejos de los compromisos definidos.
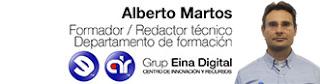